Turkey facing difficult options in eastern Mediterranean
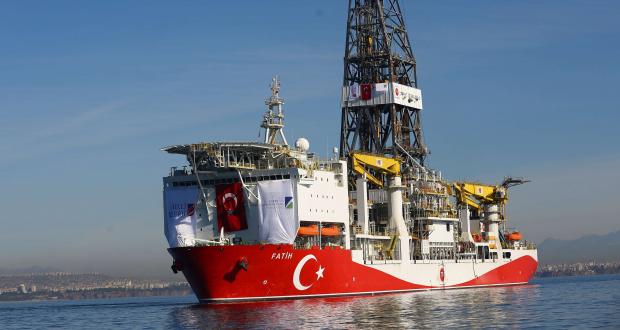
Greek Cypriot Energy Minister George Lakkotrypis last week announced a new deal that had been agreed with a consortium of three gas producing companies – Shell, Noble Energy and Israeli company Delek – also called the Aphrodite Consortium.
The earlier version of the deal provided for the extraction and sale of about 140 billion cubic metres gas to a liquefaction plant in Egypt, but the consortium was unhappy because it was based on a fixed revenue-sharing formula and on the assumption that oil prices, which are indirectly linked to the gas prices, would hover around $70 a barrel.
Some analysts disagreed with this assumption and estimated the oil prices might drop below $70 in the future. Bearing this in mind, the consortium wanted to improve the revenue-sharing arrangement of the first version of the deal.
The modified version of the deal provides that the consortium’s share will increase when the oil prices drop below $70 a barrel, and the government share will increase when oil prices go higher. In other words, the consortium wanted to guarantee its own profits and did not mind giving a bigger share to the government if prices remain high.
In exchange for this improvement, the consortium agreed to start exporting gas in 2024-25. In the first version, there was no obligation to stick to a timetable.
Lakkotrypis said Cyprus would earn $9.3 billion over 18 years. Depending on the fluctuations of the gas prices, this corresponds to about $516 million a year during the life of the project.
He may have hastened to announce this incomplete deal to send a message to Turkish Cypriots that they are going to miss an opportunity if they do not give up their insistence on shared sovereignty of the Republic of Cyprus. The deal is incomplete because the consortium has yet to find a market for gas to be liquefied in Egypt. It is not guaranteed, because the liquefied gas is up to 25 to 30 percent more expensive than the pipe-born gas.
Exploration and extraction of gas became an important subject in Greek Cypriot politics when in 2011 the U.S.-based company Noble Energy discovered rich reserves in the Aphrodite gas field off the southeast coast of the island.
The elephant in the room is Turkey.
After Lakkotrypis’ announcement, Turkish President Recep Tayyip Erdoğan last week said such agreements breach the rights of Turkish Cypriots. “Our kinsmen in northern Cyprus have rights according to international law in the same way that Greek Cypriots have. We will not allow these rights to be usurped by those who have no business (in the region).”
Turkey will likely oppose any attempt to upset the sensitive balance between Turkish and Greek Cypriots’ rights in the island. Although the Greek Cypriots acknowledge the Turkish Cypriots’ legitimate rights and say it loudly, they stop short of committing themselves to guaranteeing it in an internationally binding manner. They prefer to keep this option subject to their volition.
Lakkotrypis’ statement coincided with two other statements coming from France and the United States, and Turkey was not pleased to hear them.
French president Emmanuel Macron said on Monday that France would act in solidarity with Greece, which is threatened in the eastern Mediterranean.
The other statement came from Matthew Palmer, the deputy under-secretary in the U.S. State Department. He said the United States has 10 warships, 130 fighter aircraft and about 9,000 soldiers in the region, and criticised Turkish naval activities off the coast of Cyprus and asked for them to stop.
Both the United States and France make such statements to protect the economic interests of their companies rather than for the sake of international legitimacy.
These narratives and counter-narratives indicate that dark clouds are gathering over the eastern Mediterranean. It does not necessarily mean that a clash is likely. However, in this strained atmosphere, the best course of action for Turkey would be to explain to the international community why the Greek Cypriots have no right to ignore the Turkish Cypriots’ legitimate rights and for the Greek Cypriots, France, and the United States to understand that Turkey will not give up these legitimate rights.